10 Best Inventory Control Tools in 2025
Efficient inventory management is the backbone of any successful business operation. In a rapidly evolving market, where customer expectations for timely deliveries and accurate stock availability are higher than ever, businesses cannot afford to lag in managing their inventory. Poor inventory practices can ripple through the supply chain, causing delays, dissatisfied customers, and financial losses. On the flip side, leveraging modern inventory control tools can help businesses streamline operations, minimize costs, and maintain a competitive edge.
According to a report by Zion Market Research, the global inventory management software market is expected to reach $7.69 billion by 2032 and grow at a CAGR of 12.9% from 2024 to 2032. This growth underscores the critical role of inventory management tools in enhancing operational efficiency.

Image source: Zion Market Research
As businesses embrace digital transformation, the advancements in inventory control tools have revolutionized how companies monitor and optimize their stock levels. With real-time data, predictive analytics, and automation, businesses can now make more informed decisions, reduce errors, and respond quickly to fluctuating market demands. These tools go beyond simple stock tracking; they enable companies to manage complex supply chains, identify trends, and improve overall customer satisfaction. The integration of artificial intelligence (AI) and machine learning into inventory systems further enhances accuracy and forecasting capabilities, allowing businesses to anticipate challenges and adapt strategies in real-time.
Let’s take a closer look at the risks of inefficient inventory management and the tools that are shaping the future of inventory control in 2025.
What Are The Risks of Inefficient Inventory Management?
Inefficient inventory management presents significant risks that can undermine a company’s profitability, operational success, and customer relationships. Forbes defines inventory management as the “umbrella term for the procedures and processes that affect ordering, receiving, storing, tracking, and accounting for all of the goods a business sells.”
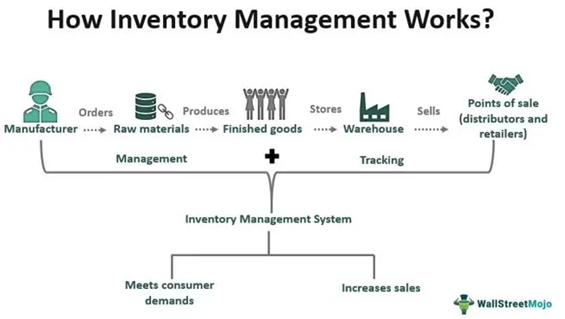
Image source: fastener shows
Overstocking, for instance, leads to inflated storage costs and increased risk of product obsolescence, especially for industries dealing with perishable goods or fast-changing technology. An overstocked warehouse not only drains financial resources but also ties up capital that could be reinvested into areas such as marketing, product development, or expanding business operations.
Conversely, stockouts can have an equally damaging impact. Running out of essential inventory disrupts order fulfillment, damages brand reputation, and often leads customers to switch to competitors. According to a study published in the Harvard Business Review, stockouts result in an estimated 4% loss of revenue annually for retail businesses. Furthermore, frequent stockouts not only hurt immediate sales but can also lead to long-term loss of customer loyalty, as frustrated customers seek more reliable alternatives.
Another critical risk is the mismanagement of expiry dates, particularly in industries like food, healthcare, and pharmaceuticals. Failing to track and rotate inventory properly can lead to wasted products, regulatory penalties, and potential harm to customers. Such mismanagement is not only financially burdensome but also poses ethical and legal risks for businesses. Implementing systems that automate expiry date tracking and batch rotation ensures compliance and minimizes waste.
Poor inventory visibility and a lack of robust analytics further exacerbate inefficiencies. Without accurate, real-time insights, businesses struggle to forecast demand accurately, often resulting in either overstocking or understocking. Ineffective forecasting can also disrupt procurement cycles, leading to strained supplier relationships and inflated costs. It is proved that improving the accuracy of inventory records can grow sales by 4-8%.
Image source: ECR Retail Loss
Manual inventory processes also leave room for significant errors. From incorrect data entry to misplaced stock, these issues create inefficiencies that ripple through the organization. In industries with complex supply chains, such as manufacturing or e-commerce, even minor inventory errors can lead to major disruptions, delays, and increased operational costs.
The absence of a well-integrated inventory management system can also hinder a business’s ability to adapt to market changes. For instance, sudden shifts in consumer demand, such as those experienced during the COVID-19 pandemic, highlighted the need for agile inventory systems capable of responding to dynamic conditions. Businesses equipped with modern inventory control tools were better positioned to navigate disruptions and meet customer needs, while those relying on outdated methods struggled to keep up.
In today’s competitive landscape, these inefficiencies can be detrimental, particularly for small and medium-sized enterprises (SMEs) that operate on tighter margins. A comprehensive and well-integrated inventory control tool is no longer a luxury but a necessity for businesses looking to optimize their operations, reduce waste, and maintain a strong market presence.
Looking For a Custom Inventory Solution?
Contact Savvycom today to build a tailored inventory system optimized for your business needs.
10 Key Inventory Control Tools
In 2025, businesses are turning to innovative inventory control tools to manage increasingly complex supply chains. These tools provide solutions to challenges like manual errors, time inefficiencies, and lack of visibility, ensuring seamless operations and improved customer satisfaction. Let’s dive into the top ten inventory management tools and their transformative impact on businesses.
Barcode Scanner
The barcode scanner remains a cornerstone of efficient inventory control tools. By automating data capture, barcode scanning eliminates human errors during inventory intake, stock checks, and shipping processes. This tool accelerates workflows, especially in large warehouses where manually tracking thousands of items is impractical. Modern barcode systems are integrated with software solutions to provide real-time updates on stock levels, improving accuracy and enabling businesses to track products across their entire lifecycle.
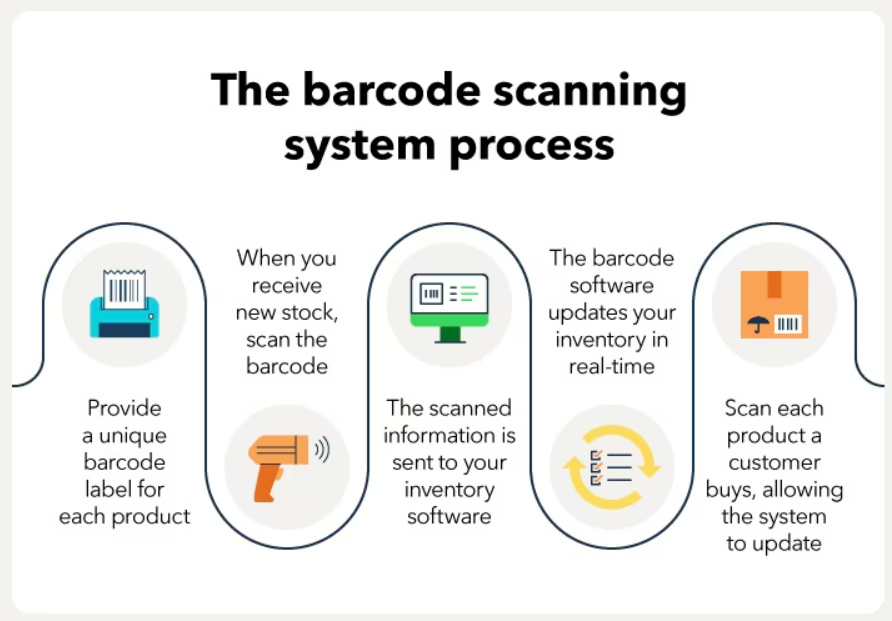
Image source: Quickbooks
Inventory Location Tracking
As warehouses and storage facilities expand, location tracking tools have become indispensable when it comes to inventory control tools. These tools assign unique identifiers to specific storage areas, bins, or shelves, making it easy for employees to locate items quickly. Advanced systems even integrate GPS technology or RFID, allowing real-time tracking across large facilities or multiple warehouses. Improved location tracking minimizes search time, reduces labor costs, and ensures orders are processed without delays, which is critical in industries like e-commerce where speed is a competitive advantage.
Tracking Serial Numbers, Batches, and Expiry Dates
Tracking serial numbers, batches, and expiry dates is particularly essential for businesses dealing with perishables, pharmaceuticals, or high-value items. This inventory control tool ensures traceability, compliance, and quality control by linking products to their manufacturing details and expiration timelines. For example, if a defect is identified in a specific product batch, businesses can quickly trace and recall it without disrupting their entire supply chain. For this process, businesses should automate rather than manual tracking to reduce spoilage and manage recalls efficiently. This practice is is also part of the due diligence companies must undertake to comply with regulations and industry standards legal requirements.
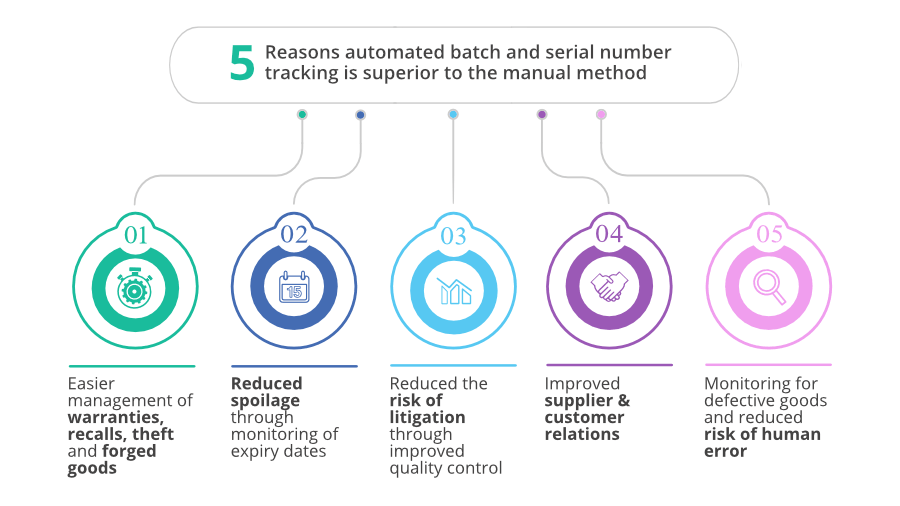
Image source: Erplain
Kit Inventory Tracking
For businesses assembling multiple components into a single product (e.g., electronics, machinery, or gift baskets), kit inventory tracking is a game-changer as a inventory control tool. This tool tracks the availability of all required components, ensuring they are assembled correctly and on time. By offering a complete view of component stock levels, kit tracking prevents production delays and ensures customer orders are fulfilled accurately. Users can easily select different inventory items and combine them into one overall group.
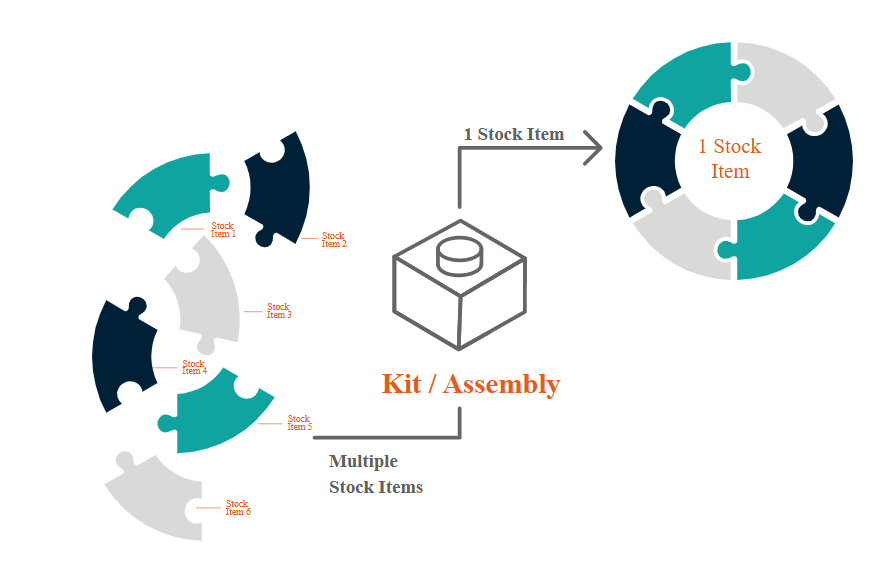
Image source: ASAP
Low Stock Alerts
Running out of stock is a nightmare for any business, leading to lost sales and frustrated customers. Low stock alert systems provide proactive notifications when inventory levels fall below a predefined threshold. These inventory control tools enable businesses to reorder supplies before stockouts occur, ensuring uninterrupted operations. Low stock alerts are particularly useful in fast-moving industries like retail or food services, where demand fluctuations can be sudden.
Purchase Order Management
Efficient purchase order management tools streamline procurement processes by automating order creation, tracking, and approval. These inventory control tools and systems ensure that purchase orders are accurate, delivered to the right suppliers, and aligned with inventory needs. By integrating with other inventory control tools, purchase order systems prevent overordering or underordering, reducing waste and maintaining optimal stock levels. Some tasks that are typically automated in a purchase order process include:
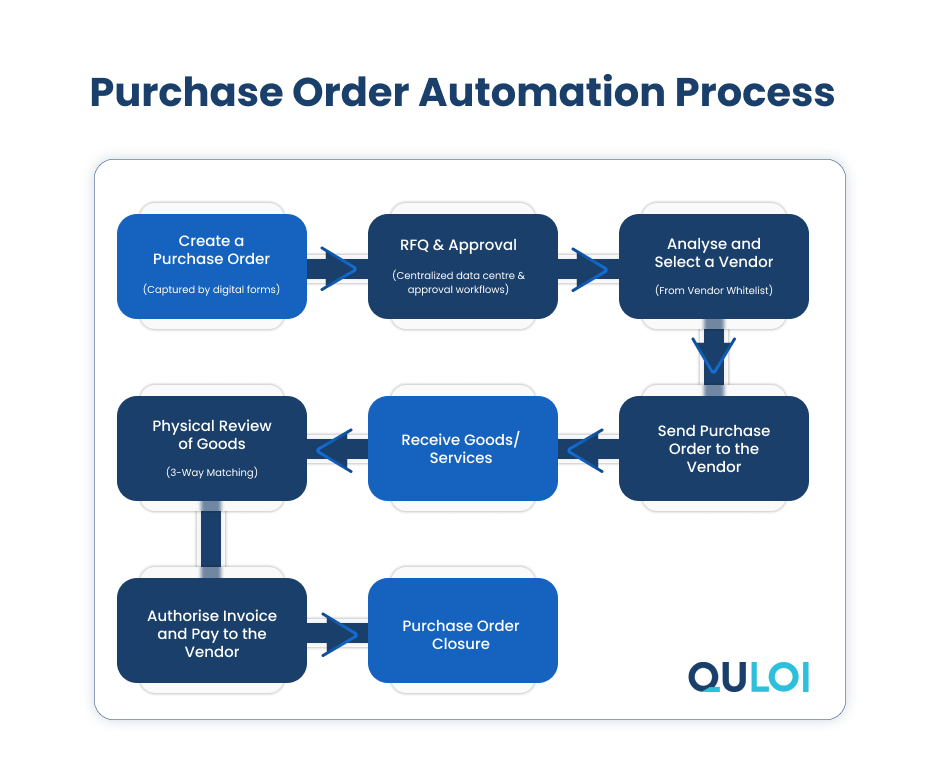
Image source: Quloi
Dashboard for Quick Analysis
Modern inventory control tools and systems come equipped with intuitive dashboards that provide a snapshot of key performance indicators (KPIs). Dashboards display metrics such as stock levels, sales trends, and inventory turnover rates, enabling managers to make data-driven decisions. Customizable dashboards cater to specific business needs, offering a real-time view of operational performance. In an era where agility is vital, dashboards empower businesses to identify trends and respond quickly to changes in market demand.
Reports
Comprehensive reporting tools are essential for evaluating inventory performance and identifying areas for improvement. These inventory control tools generate detailed reports on stock movements, order histories, and supplier performance, helping businesses optimize their inventory practices. Advanced reporting systems even incorporate predictive analytics, allowing companies to forecast demand and align their procurement strategies accordingly. Businesses using data-driven reports are often better positioned to reduce costs and maximize profitability.
Multi-location Management
For businesses with operations spread across multiple warehouses, stores, or distribution centers, multi-location management tools are crucial. These inventory control tools and systems centralize inventory data from different locations, providing a unified view of stock availability and movement. By enabling inter-location transfers and real-time tracking, multi-location management tools improve inventory visibility and prevent stockouts or overstocking at specific sites. They also support regional demand forecasting, ensuring that the right inventory is available at the right location.

Image source: Apimio
Integration with Other Management Systems
Integration capabilities are perhaps the most critical feature of modern inventory control tools. By syncing with systems like Enterprise Resource Planning (ERP), Customer Relationship Management (CRM), and e-commerce platforms, inventory control tools ensure seamless data flow across business operations. This integration eliminates silos, enhances collaboration between departments, and provides a holistic view of inventory management. For example, integrating inventory tools with a CRM system allows sales teams to check stock availability in real-time, improving customer service.
Each of these inventory control tools plays a vital role in optimizing inventory management processes. Together, they enable businesses to stay competitive in a demanding marketplace by reducing inefficiencies, improving accuracy, and enhancing decision-making capabilities. As inventory control tools continue to evolve, companies that adopt and integrate these technologies will be better equipped to thrive in 2025 and beyond.
FAQs
1. What are inventory control tools?
Inventory control tools are software and systems that help businesses manage stock levels, track inventory movement, and streamline procurement processes. These tools include barcode scanners, real-time dashboards, expiry tracking systems, and more.
2. Why is inventory control important in 2025?
With rising customer expectations and globalized supply chains, efficient inventory control in 2025 is critical to prevent overstocking, reduce waste, minimize stockouts, and ensure real-time visibility.
3. Which features should businesses look for in inventory control tools?
Key features include barcode scanning, multi-location management, expiry tracking, purchase order automation, low-stock alerts, real-time dashboards, and integration with ERP/CRM systems.
4. How do inventory tools help reduce costs?
By improving stock accuracy, minimizing over-ordering or under-ordering, and automating manual processes, inventory tools help cut operational costs, reduce waste, and optimize supply chain efficiency.
5. Can small businesses benefit from inventory control software?
Yes. Many inventory control tools are scalable and offer tailored solutions for SMEs, allowing them to improve accuracy, save time, and compete effectively in fast-moving industries.
Savvycom’s Role in the Retail Industry
The retail industry faces unique challenges, including fluctuating consumer demand, high competition, and the need for seamless operations across multiple sales channels. Recognizing these complexities, Savvycom offers tailored software solutions that address the most pressing pain points in the retail ecosystem.
Specifically, we provide tailored solutions to help retailers manage their inventory more efficiently. With our advanced ERP system, SavvyERP, retailers can streamline their inventory processes, ensuring accurate stock levels and reducing operational costs. We also offer customized dashboards and reporting tools, providing real-time insights into inventory performance and trends. Additionally, our solutions include barcode scanning systems that simplify stock tracking and improve accuracy, allowing retailers to enhance operational efficiency and customer satisfaction.
Tech Consulting, End-to-End Product Development, Cloud & DevOps Service! Since 2009, Savvycom has been harnessing digital technologies for the benefit of businesses, mid and large enterprises, and startups across the variety of industries. We can help you to build high-quality software solutions and products as well as deliver a wide range of related professional services.
Savvycom is right where you need. Contact us now for further consultation:
- Phone: +84 24 3202 9222
- Hotline: +1 408 663 8600 (US); +612 8006 1349 (AUS); +84 32 675 2886 (VN)
- Email: [email protected]