The Ultimate Guide to MES in Manufacturing for Efficiency and Productivity
Manufacturing Execution Systems (MES) have become pivotal in modern manufacturing, bridging the gap between enterprise resource planning (ERP) systems and the shop floor. By providing real-time monitoring, control, and optimization of production processes, MES in manufacturing enhances efficiency and productivity. This comprehensive guide delves into the core aspects of MES in manufacturing, exploring its benefits, implementation strategies, and best practices.
Understanding MES in Manufacturing
An MES is an information system that connects, monitors, and controls complex manufacturing systems and data flows on the factory floor. Its primary goal is to ensure effective execution of manufacturing operations and improve production output. By capturing real-time data from machines, operators, and other resources, MES provides a holistic view of manufacturing activities, enabling informed decision-making and swift response to changing conditions.
Key Benefits of Implementing MES in Manufacturing
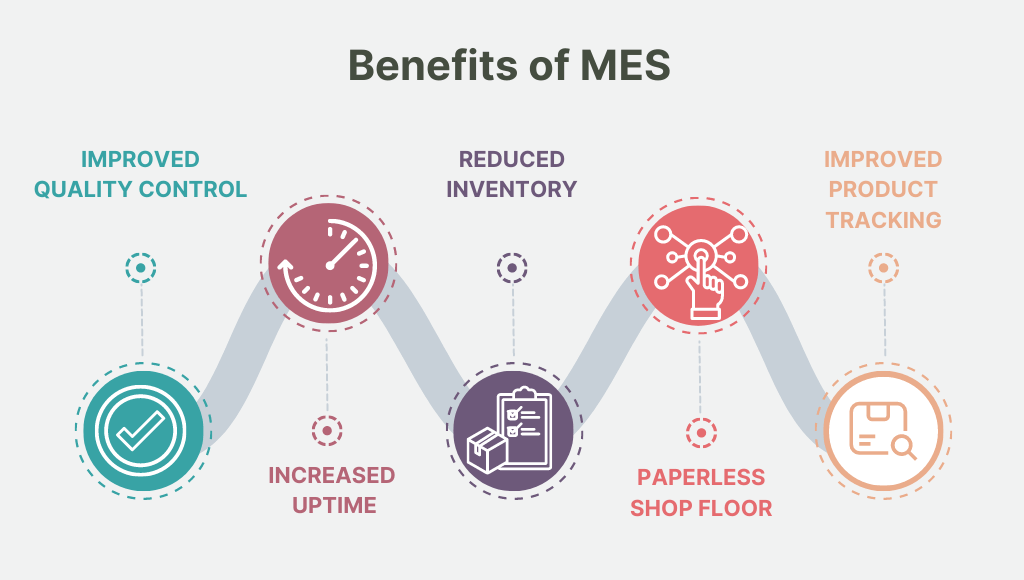
Image source: leanonus
1. Improved Production Efficiency
MES in manufacturing offers real-time visibility into production processes, allowing manufacturers to identify and address bottlenecks promptly. By automating scheduling and resource allocation, MES reduces downtime and enhances throughput.
2. Enhanced Quality Control
By monitoring production parameters and enforcing quality standards, MES in manufacturing ensures that products meet specified criteria. Real-time data collection facilitates immediate detection of deviations, reducing defects and rework.
3. Real-Time Data and Analytics
MES in manufacturing provides actionable insights through real-time data collection and analysis. Manufacturers can track key performance indicators (KPIs) such as cycle times, yield, and equipment effectiveness, enabling data-driven decisions that enhance operational efficiency.
4. Inventory Management and Supply Chain Optimization
Integrating MES in manufacturing with supply chain management systems improves inventory accuracy and reduces carrying costs. MES tracks material usage and product genealogy, facilitating just-in-time inventory practices and enhancing coordination with suppliers and customers. This integration can result in a 20% reduction in inventory costs.
5. Increased Agility and Flexibility
MES in manufacturing enables manufacturers to adapt quickly to changes in demand, production schedules, and product designs. This agility is crucial in today’s dynamic market environment, allowing companies to introduce new products faster and respond effectively to customer needs.
Looking For a Trusted Tech Partner?
We’ll help you decide on next steps, explain how the development process is organized, and provide you with a free project estimate.
Key Components of MES
An effective MES in manufacturing encompasses several core components:
-
Resource Allocation and Status: Manages resources, including machinery and labor, ensuring optimal utilization.
-
Operations Scheduling: Plans and sequences production activities to meet delivery deadlines efficiently.
-
Dispatching Production Units: Coordinates the release of production orders to the shop floor in a timely manner.
-
Data Collection: Gathers real-time data from various production processes for analysis and reporting.
-
Quality Management: Monitors and controls product quality during manufacturing to reduce defects and rework.
-
Process Management: Oversees manufacturing processes to ensure consistency and adherence to standards.
-
Performance Analysis: Evaluates production performance metrics to identify areas for improvement.
-
Document Control: Manages and controls access to manufacturing documents and specifications.
Implementing MES in Manufacturing: A Step-by-Step Approach
Successful MES implementation requires careful planning and execution:

Image source: Codeit
1. Conduct a Thorough Needs Analysis
Before selecting an MES in manufacturing, assess your organization’s specific requirements. Identify pain points in current processes and define clear objectives for the MES implementation. Engage stakeholders from various departments to ensure comprehensive understanding and alignment.
2. Engage Key Stakeholders
Successful MES implementation requires buy-in from all levels of the organization. Involve operators, IT personnel, and management early in the process to address concerns, gather insights, and foster a collaborative environment.
3. Develop a Comprehensive Implementation Plan
Create a detailed roadmap outlining each phase of the MES implementation. Set realistic timelines, allocate resources appropriately, and establish metrics to measure progress and success.
4. Provide Adequate Training and Support
Invest in training programs to equip employees with the necessary skills to operate and leverage the MES in manufacturing effectively. Continuous support and refresher courses can help maintain proficiency and adapt to system updates.
5. Monitor and Measure Effectiveness
After implementation, continuously monitor the MES in manufacturing’s performance against predefined metrics. Gather feedback from users and make adjustments as needed to optimize system functionality and achieve desired outcomes.
Overcoming Challenges in MES Implementation
Implementing an MES in manufacturing can present challenges:
-
High Initial Investment: The upfront costs can be substantial, but the long-term benefits often justify the expenditure.
-
System Integration: Ensuring compatibility with existing systems requires meticulous planning and expertise.
-
Change Management: Addressing resistance to change through effective communication and training is crucial for successful adoption.
MES and Emerging Manufacturing IT Trends
The landscape of manufacturing IT trends is evolving, with MES playing a central role in several key trends:
Integration with IIoT
The Industrial Internet of Things (IIoT) enhances MES capabilities by enabling seamless communication between devices and systems. This integration facilitates advanced data analytics and predictive maintenance strategies.
Cloud-Based Solutions
Cloud computing offers scalable and flexible MES solutions, reducing the need for extensive on-premises infrastructure. Quality Control, Computer-Aided Engineering, and Manufacturing Execution Systems (MES) are the three most widely adopted systems in the cloud by discrete and process. Survey also found that 60% of discrete and process manufacturers say their end users prefer the cloud over on-premise.
Artificial Intelligence and Machine Learning
Incorporating AI and machine learning into MES in manufacturing allows for enhanced data analysis, pattern recognition, and decision-making support, leading to improved process optimization and quality control. Notably, 38% of manufacturers plan to invest in AI and machine learning capabilities within their MES. Worldmetrics
Mobile Accessibility
Mobile-enabled MES applications provide operators and managers with real-time access to production data, facilitating prompt decision-making and increased responsiveness on the shop floor.
Conclusion
Implementing an MES in manufacturing is a strategic move towards achieving enhanced efficiency and productivity. By understanding its components, benefits, and implementation strategies, manufacturers can make informed decisions that drive operational excellence. Embracing MES not only streamlines production processes but also positions organizations to adapt to future manufacturing IT trends and maintain a competitive edge.
As a leading software development company, Savvycom specializes in delivering manufacturing solutions tailored to modern industry needs. Our expertise in software design for manufacturing ensures seamless integration of MES with existing enterprise systems like ERP and CRM, optimizing production efficiency.
With a commitment to innovation, we help businesses adopt cutting-edge manufacturing IT trends, ensuring they stay ahead of the competition. Whether you’re looking to implement MES, integrate RPA in manufacturing, or leverage advanced analytics, Savvycom provides end-to-end support to enhance your manufacturing processes.
Contact us today to explore how we can help you achieve operational excellence with MES!
Tech Consulting, End-to-End Product Development, Cloud & DevOps Service! Since 2009, Savvycom has been harnessing digital technologies for the benefit of businesses, mid and large enterprises, and startups across the variety of industries. We can help you to build high-quality software solutions and products as well as deliver a wide range of related professional services.
Savvycom is right where you need. Contact us now for further consultation:
- Phone: +84 24 3202 9222
- Hotline: +1 408 663 8600 (US); +612 8006 1349 (AUS); +84 32 675 2886 (VN)
- Email: [email protected]